explain the process of making metal sheets Below, we’ll explain the most common metal manufacturing processes: Cutting. The first step in the sheet metal fabrication process is cutting, which is where the fabricators will slice the raw . $79.99
0 · various sheet metal processes
1 · types of sheet metal process
2 · types of sheet metal fabrication
3 · sheet metal working process pdf
4 · sheet metal process pdf
5 · sheet metal process in manufacturing
6 · sheet metal operations with diagrams
7 · sheet metal fabrication pdf
$64.95
There are four basic stages in the process of making sheet metal: melting, pouring, pickling and lastly, rolling and annealing. Sheet metal is made for a wide range of purposes, from automotive parts to rain gutters to medical equipment and building components.
Embossing. Spinning. Stamping. The family of manufacturing processes used to create sheet metal components encompasses a diverse range of techniques, each tailored to achieve specific shapes, sizes, and features with precision .Below, we’ll explain the most common metal manufacturing processes: Cutting. The first step in the sheet metal fabrication process is cutting, which is where the fabricators will slice the raw .
The sheet metal fabrication process is an intricate journey from raw metal to a finished product. It involves various steps, ensuring the final product meets specific standards and functions. In .The Sheet Metal Manufacturing Process. 1. Design. The design process is conducted by engineers who work diligently to ensure that the idea put down on paper will result in a product .
The process of producing sheet metal components using metal sheets is known as sheet metal forming or sheet metal fabrication. This is accomplished by bending, punching, shearing, hydroforming, and other . For the shearing process in sheet metal, sheets are fabricated into multiple components – all of which can now be used to manufacture different items. The metal material itself is cut precisely and accurately, with the .a) With a schematic (diagram), explain the shearing mechanism in sheet metal forming (10 points) minimum 5 bullet points b) List two methods to achieve a burr free sheet metal ( 5 points [2.5 points each for the correct answeri) C) Why does barreling happen in open die forging ( 2.5 points) How can we reduce it? (2.5 points) d) Why are drawbead . Sheet metal forming is a process used in many industries to make metal parts from thin metal sheets. It’s actually one of Xometry's most popular manufacturing methods. Our customers use the Xometry Instant Quoting .
Aluminium Plate is made by passing the metal through high pressure rollers so the metal is forced into a thinner, longer shape, a remarkably simple process that is also used to create Aluminium Sheet and Aluminium Foil.. Here are some key details. Aluminium plate, foil and sheet thicknesses. Unlike many metals, which fatigue more easily, it is perfectly possible to roll .
If the metal is overpinched between the two working surfaces, it might prevent the metal from flowing, resulting in excessive stretching and possible splitting of the metal. The drawing process is used to make thousands of different common parts, such as oil filters, deep-formed auto parts, kitchen sinks, cookware, motorcycle gas tanks, and . The steel metal fabrication process can differ from case to case depending on the requirement of the design specifications, but the typical fabrication process remains the same. Let us explain the steps involved in the sheet metal fabrication process: Designing: The sheet metal fabrication process begins by creating a design of the product need . The metal drawing process is a fundamental manufacturing technique that transforms metal materials into desired shapes and structures through the application of force. Widely used in various industries, such as automotive, aerospace, and construction, metal forming encompasses a diverse range of methods, including bending, stamping, rolling .
The most common process for iron ore-based steel production in the world is the blast furnace–basic oxygen furnace (BF–BOF) route, but there is also the less common direct reduced iron .
The shearing force applied during this process subjects the sheet metal under stress and once the material’s ultimate shear strength is overcome, the material is cut. There are different methods to mechanically cut sheet metal but the basic concept uses cutting blades between the material. The equipment for this process can be operated in .The deburring process in sheet metal processing is vital to ensure safety and the overall finish of the final product. This step involves removing any sharp edges or “burrs” left from the previous processes such as cutting or punching. Edge Rounding: This is the process of eliminating sharp edges on metals. This is crucial as it helps . The fundamental goal of sheet metal forming procedures is to give the metal sheets particular geometrical modifications while preserving their structural integrity. The common types of sheet metal operations are shearing, blanking, punching, piercing, trimming, drawing, embossing, bending, and squeezing operations. Learn about sheet metal here!In this article we will discuss about the sheet metal manufacturing process and its operation types. Introduction to Sheet Metal Work: Most of the sheet metal work is done on presses where a die and punch or other formed tools are required. In press work large force is applied on thin sheet metals to give the required shape or to cut it in to the desired shape. Press work is highly .
Steel Manufacturing Process. The steel manufacturing process can be divided into six steps: Making the iron, primary steelmaking, secondary steelmaking, casting, primary forming, and secondary forming. Step 1: Making the Iron. Steel is a metal alloy made of iron and carbon. Thus, the steel manufacturing process starts by making iron.Protecting metal from corrosion is crucial for ensuring long-term durability and performance. Galvanization plays a vital role in this. Galvanization applies a protective zinc coating to steel or iron to prevent rust and corrosion, making it an essential technique in the construction, automotive, and manufacturing industries.. This guide explains the basics of galvanization, the .Study with Quizlet and memorize flashcards containing terms like 13.12 Explain why the rolling process was invented and developed., 13.13 Flat rolling reduces the thickness of plates and sheets. It is possible, instead, to reduce their thickness simply by stretching the material? Would this be a feasible process? Explain., 13.14 Explain how the residual stress patterns shown in .
electrical armored cable to plastic box
The sheet metal stamping process is a strategic advantage that can set your business apart. Precision, efficiency, and innovation are at its core, driving the production of high-quality components. In this guide, we will explore the 7 pivotal steps in sheet metal stamping. Each step is a piece of a larger puzzle that, when completed, represents .Explain the process of smelting iron. Explain the process of steel making; Solution: An iron-ore is a mineral substance that, when heated, yields metallic iron. Smelting of iron-ore is heating up the mineral with coal and limestone in an industrial oven to extract the iron. Molten iron is purified and converted into steel in a basic oxygen .Hydroforming (Sheet Hydroforming) is a specialized deep draw process that uses high-pressure rubber to shape and form metal workpieces. In sheet hydroforming, a metal sheet is placed over a die before highly pressurized water forces it down and makes it conform to the shape of the mold. This process produces high-quality steel and is commonly used for mass production. Electric Arc Furnace (EAF): EAFs use electrical energy to melt scrap steel or other sources of iron, such as direct-reduced iron. This method is more flexible and can produce smaller batches of steel, making it suitable for specialized alloys and recycling.
A sheet metal component is required to have a high quality edge, (both smooth and close to perpendicular to the surface of the sheet). Briefly discuss the relative merits of 'fine blanking' and standard blanking followed by a 'shaving' operation., Name the last shearing operation to occur in the production process using transfer dies. and more. You can make a stainless steel sheet. At the same time, the process produces many stainless steel finishes. Usually, rollers with small diameters are a perfect choice for the stainless steel cold rolling process. Stainless Steel Recrystallization Annealing Stainless Steel. During the annealing process, you will use reasonable heat to treat .When required, blanking is the first step of the stamping process. It cut the larger sheet metal or coils into small pieces, to get manageable pieces. In addition, blanking is also the last step of the stamping process, usually performed when a stamped metal piece be formed. It separates the useful parts from the scrap, or it cuts the final product from the entire metal strip (common in .

It is a sheet metal process done to the edge of the sheet, whether creating a 90-degree angle and a T-shaped corner in the sheet or making the sheet’s edge thinner by making it thinner as it crosses over itself. Conclusion. Sheet metal processing is a vital part of the metal machining industry. Though it might seem simple, the work has high . A complete list of hemming benefits on a sheet metal product is as follows: Hems strengthen the sheet metal edge. They improve the surface appearance and surface quality. They hide defects such as rough edges and burrs. They can connect parts. They make the edges safer to handle. Hem Types. The different sheet metal hems based on the hem shape .Study with Quizlet and memorize flashcards containing terms like How does sheet-metal forming differ from rolling, forging, and extrusion?, Explain the difference between punching and blanking., Define normal anisotropy, and explain why it is important in determining the deep drawability of a material. and more.
Metal prints are a variation of traditional printing styles that imbue color into metal materials (usually aluminum) to create a durable display. The most common printing technology used to print metal prints is dye sublimation, which helps ensure the final result is as accurate as possible. Metal print sizes come in sizes limited by what Machining is a critical process in sheet metal fabrication that involves the removal of material from a workpiece to achieve the desired shape and dimensions. Unlike forming processes, machining provides high precision and is essential for creating intricate details and features on metal components. .
various sheet metal processes
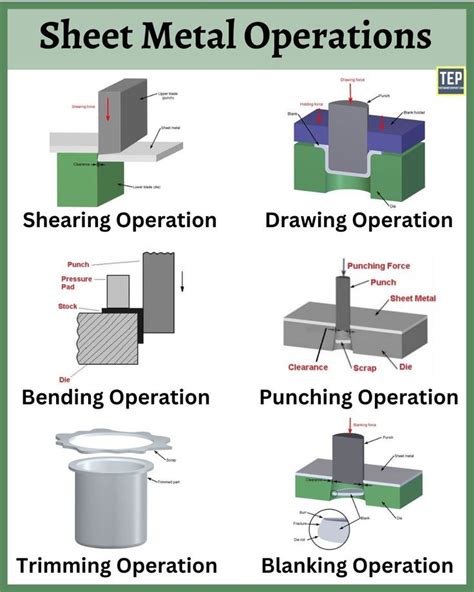
Get the best deals on Xbox One S SteelBook Original Video Game Cases & Boxes when you shop the largest online selection at eBay.com. Free shipping on many items | Browse your .
explain the process of making metal sheets|types of sheet metal process